The Scientific Research Behind Porosity: A Comprehensive Overview for Welders and Fabricators
Understanding the complex systems behind porosity in welding is critical for welders and producers striving for flawless craftsmanship. From the make-up of the base materials to the details of the welding process itself, a plethora of variables conspire to either aggravate or reduce the visibility of porosity.
Recognizing Porosity in Welding
FIRST SENTENCE:
Evaluation of porosity in welding discloses important insights into the integrity and quality of the weld joint. Porosity, defined by the existence of dental caries or voids within the weld metal, is a typical issue in welding procedures. These voids, if not appropriately resolved, can endanger the structural honesty and mechanical buildings of the weld, leading to prospective failings in the ended up item.
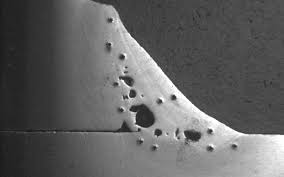
To find and measure porosity, non-destructive testing methods such as ultrasonic testing or X-ray assessment are usually employed. These techniques permit the identification of internal issues without jeopardizing the honesty of the weld. By assessing the dimension, shape, and distribution of porosity within a weld, welders can make enlightened choices to boost their welding processes and attain sounder weld joints.
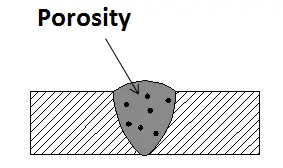
Variables Influencing Porosity Development
The event of porosity in welding is affected by a myriad of aspects, varying from gas protecting efficiency to the intricacies of welding parameter settings. One vital aspect adding to porosity formation is inadequate gas shielding. When the shielding gas, normally argon or CO2, is not efficiently covering the weld pool, atmospheric gases like oxygen and nitrogen can infect the liquified metal, bring about porosity. Furthermore, the sanitation of the base materials plays a substantial function. Pollutants such as corrosion, oil, or wetness can vaporize throughout welding, creating gas pockets within the weld. Welding specifications, including voltage, existing, take a trip speed, and electrode kind, likewise effect porosity development. Using improper settings can generate too much spatter or warm input, which subsequently can lead to porosity. Additionally, the welding strategy used, such as gas steel arc welding (GMAW) or protected metal arc welding (SMAW), can from this source affect porosity development due to variants in warm circulation and gas protection. Understanding and regulating these elements are essential for decreasing porosity in welding operations.
Impacts of Porosity on Weld Quality
The visibility of porosity also damages the weld's resistance to deterioration, as the caught air or gases within the voids can respond with the surrounding atmosphere, leading to destruction over time. In addition, porosity can prevent the weld's capability to withstand stress or impact, more threatening the general high quality and dependability of the welded structure. In essential applications such as aerospace, vehicle, or architectural building and constructions, where security and toughness are paramount, the damaging results of porosity on weld top quality can have serious repercussions, stressing the importance of reducing porosity via correct welding strategies and treatments.
Strategies to Decrease Porosity
Furthermore, using the proper welding criteria, such as more the appropriate voltage, current, and travel speed, is critical in protecting against porosity. Preserving a constant arc size and angle during welding likewise aids lower the possibility of porosity.

Using the suitable welding strategy, such as back-stepping or utilizing a weaving motion, can also aid distribute heat evenly and lower the possibilities visit their website of porosity development. By carrying out these strategies, welders can successfully minimize porosity and produce high-quality bonded joints.
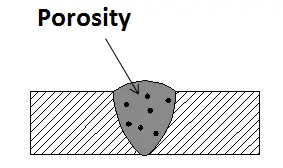
Advanced Solutions for Porosity Control
Carrying out cutting-edge modern technologies and innovative approaches plays an essential function in achieving superior control over porosity in welding procedures. In addition, using advanced welding methods such as pulsed MIG welding or modified ambience welding can also assist minimize porosity issues.
An additional sophisticated remedy involves using sophisticated welding equipment. Utilizing equipment with integrated attributes like waveform control and innovative power sources can enhance weld top quality and reduce porosity threats. The application of automated welding systems with precise control over criteria can significantly reduce porosity defects.
Moreover, incorporating advanced surveillance and examination technologies such as real-time X-ray imaging or automated ultrasonic testing can assist in spotting porosity early in the welding procedure, permitting instant restorative activities. On the whole, incorporating these advanced solutions can substantially enhance porosity control and improve the overall high quality of bonded components.
Final Thought
In final thought, comprehending the science behind porosity in welding is necessary for welders and fabricators to produce high-grade welds - What is Porosity. Advanced remedies for porosity control can additionally improve the welding procedure and make sure a solid and reliable weld.